What Is Concurrent Engineering
Concurrent engineering is a method by which several teams within an organization work simultaneously to develop new products and services. By engaging in multiple aspects of development concurrently, the amount of time involved in getting a new product to the market is decreased significantly.
Concurrent engineering can be applied to any industry, and by organizations of various sizes. Polaroid, Boeing, NASA, and the European Space Agency are among the most well-known entities that have successfully implemented concurrent engineering programs. In one notable example, General Electric employees were able to reduce the design time associated with several aircraft engine components by approximately 19 weeks through the use of concurrent engineering.As along, Accelerating innovative products and increasing the number of new product introductions is a huge challenge for most organizations. Here comes product life cycle management .so, what is product life cycle management? Product Life cycle Management is a process used to manage the data and design process associated with the life of a product from its conception and envisioning through its manufacture, to its retirement and disposal. PLM manages data, people, business processes, manufacturing processes, and anything else pertaining to a product. A PLM system acts as a central information hub for everyone associated with a given product, so a well-managed PLM system can streamline product development and facilitate easier communication among those working on/with a product.
The various functions that go into the Product life cycle management are as follows. Core PLM for both discrete and process industries, Engineering Change Management, Data Vaulting, BOM Management, Product Cost Estimation, Product Development and Portfolio Management, Manufacturing Process Management (MPM), Ideation & Requirements Management, Service Data Management, Regulatory and Compliance and Application Technology Concurrent engineering focuses on the improvement of overall processes of the system, both product and process design run in parallel and occur in the…
How Toyota’s product design and development process helps find the best solutions and develop successful products.
advertisement
Toyota Motor Corporation is an industry leader in product development lead time while using fewer engineers than its U.S. competitors. It has also shown remarkable consistency in market share growth and profit per vehicle, which led to cash reserves of $21 billion, exceeding those of the “Big Three” automakers combined.1 The Toyota Production System (TPS), dubbed “lean manufacturing,” has been critical in these accomplishments,2 but we believe that Toyota’s product design and development system is also an important contributor.3
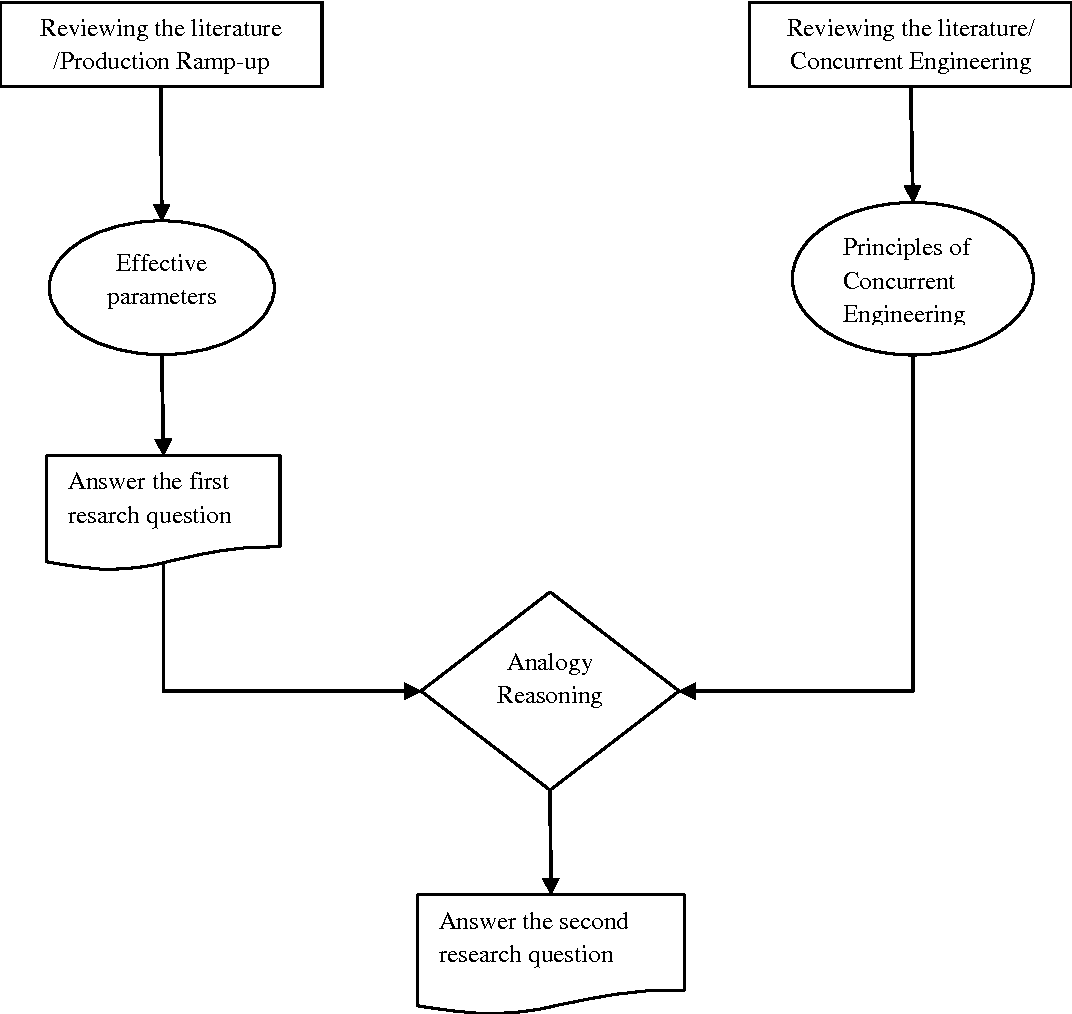
While Taiichi Ohno and others have meticulously described the TPS, the Toyota development system has not been well documented.4 Indeed, Toyota does not use many of the practices often considered critical to successful concurrent engineering and associated with Japanese manufacturers. Its development teams are not colocated. Personnel, with the exception of the chief engineer and his staff, are not dedicated to one vehicle program. Cross-functional job rotation is unusual for the first ten to twenty years of an engineer’s career. Engineering and test functions rarely use quality function deployment (QFD) and Taguchi methods. Toyota excels at value engineering (VE) and value analysis (VA), yet Toyota engineers say they do not use any of the text-book tools and matrices for VE or VA. And there is nothing remarkable about Toyota’s CAD or CAE systems. These practices, then, do not explain Toyota’s effectiveness in developing new vehicles.
In a previous article, we called Toyota’s product development system the “second Toyota paradox.”5 TPS was the first; its features seem wasteful but result in a more efficient overall system, such as changing over manufacturing processes more frequently (presumably inefficient) in order to create short manufacturing lead times. The second paradox can be summarized in this way: Toyota considers a broader range of possible designs and delays certain decisions longer than other automotive companies do, yet has what may be the fastest and most efficient vehicle development cycles in the industry.
Traditional design practice, whether concurrent or not, tends to quickly converge on a solution, a point in the solution space, and then modify that solution until it meets the design objectives. This seems an effective approach unless one picks the wrong starting point; subsequent iterations to refine that solution can be very time consuming and lead to a suboptimal design.
Read the Full Article:
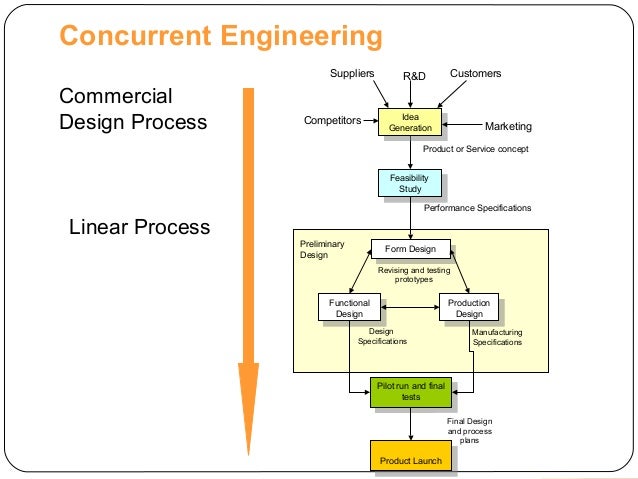

Sign in, buy as a PDF or create an account.